Bangladesh is Set to Build Roads Using Recycled Plastic

As a solution to plastic waste generation and its dire impact on the environment, the government of Bangladesh is opting to recycle waste plastics in the construction of roads. Already a practice in many other countries, this initiative by the Roads and Highways Department (RHD) of Bangladesh is to be set in motion in (hopefully the beginning of) 2023.
RHD is reportedly preparing provisions for designs and durability testing for the proposed roadways. Upon completion, the plastic roads are to be tested on national and regional highways and in hilly regions.
Work in Progress
The RHD team requires information on the types of plastics disposed of in different locations. A study team from the University of Texas at Arlington in the United States is already collaborating with the RHD to assess solid waste material in the country.
So far, 17 roadside solid waste disposal locations in Bangladesh have been characterised, and the task of defining quality requirements is well underway.
The trial and installation procedures are nearing completion, and the organized test will be launched soon in several areas based on differing climate conditions, exposures to hazards, and traffic loading dynamics. The RHD team is also working on a variety of grades of plastics to use with road construction materials.
Problems with the Road Infrastructure in Bangladesh
In Bangladesh’s 21,000 kilometres of highways and over 350,000 kilometres of public roadways, the most common type of pavement you’ll find yourself traipsing on is the one with a pliable bitumen coating. Here, the uppermost layers incorporate several loose layers of robust materials. But there’s usually some problem with the foundation and surfacing materials.
On the base layer, the unavailability of crushed rock necessitates the use of crushed brick, a softer material, instead. And because of insufficient finances, thin bitumen sheets are used in the surfacing. So, the upper layers are delicate and usually vulnerable to the loads imposed by vehicles and adverse environmental conditions such as heavy rainfall, heat, and humidity, causing fractures and breakage on the roads soon after their construction.
Also, Dhaka roadways are frequently dug shortly after construction to relocate or repair underground infrastructure facilities such as gas, water supply, or telephone lines.
Under these circumstances, it’s safe to say that potholes and waterlogged roads are a constant in the lives of people.
Plastic Road Benefits
World Population Review 2022 listed Bangladesh among the top 10 countries that released the highest amounts of plastic into the ocean in 2021 (24,640 tons). The total amount of plastic waste generated by the country in 2021 was 1,021,990 tons. Recycling this waste plastic to make roads can therefore quite obviously help protect the environment.
Roads made from recycled plastics have a far lower carbon footprint than conventional roads which generate more than 1.6 million tons of carbon dioxide into the environment annually.
The plastic-asphalt mix requires lower operating temperatures, 20% less fuel for production, and fewer vapors generated during the application process. In addition to this, mixing plastic with asphalt reduces bitumen usage by 15%. This process also requires less transportation movement.
According to experts, besides its “green” appeal, plastic roads can solve Bangladesh’s age-old problem of damaged and waterlogged roads.
As opposed to asphalt roads, plastic roads are better at withstanding high temperatures and intense rainfall, conditions that are the leading contributors to road breakage. Plastic roads can endure heat until the temperature exceeds 66°C, which is greater than the minimum temperature of 50.2 °C for traditional roads.
Experts say that polymer-modified bitumen, i.e., a combination of bitumen, sand, stone, etc., and polymer paste derived from disintegrated plastic wastes makes roadways more sustainable.
Furthermore, plastic roads take one-third the amount of time needed to build asphalt roads, saving a lot of time that is otherwise used up in blocking roadways due to construction.
Engineering experts also suggest developing walking pavements from plastic because they will make it easier to repair underground utility systems without excavating roadways.
From a construction viewpoint, building plastic roads entails premade, lightweight, and hollow road construction made out of plastic. This structure, compared to bituminous road systems, allows for easier and faster construction of roads.
An example of Jambulingam Street, located in Chennai, India, highlights how the plastic roads proved to be beneficial for the localities. Being one of the first plastic roads built in India, these roads have remained sturdy for several years now, with no cracks, deformations, or edge defects yet.
How Plastic Roads Are Made
The first stage in building these roads involves collecting and managing the plastic. The plastics used are mostly discarded household plastics such as product packaging. Polyethylene terephthalate (PET or PETE), polypropylene (PP), and high- and low-density polyethylene (HDPE and LDPE) are some of the most commonly used polymers.
Plastic roads can be constructed using either of the two methods: the wet process and the dry process.
In the dry process, polymer components are first separated from plastic waste and then cleaned, dried, and shredded after sorting. At roughly 165 °C, the shredded plastic is blended and melted. The molten plastic is then combined with hot bitumen. Finally, the resulting mixture is set in the same manner as traditional asphalt pavement.
Are Plastic Roads Cheaper?
The cost-effectiveness of plastic roads for Bangladesh will depend on factors such as where the plastic will be sourced from and how.
The process that will be employed to build the roads is a major factor in determining the cost.
As described earlier, the dry process involves heating shredded plastic and combining it with stone aggregates and hot bitumen.
The wet process, on the other hand, requires the use of liquid plastic, which is costlier than shredded plastic. The expense will be higher if the liquid plastic to be used in road construction is imported. Employing the wet process will also require huge capital and equipment to complete the construction.
So when compared, the dry process is cheaper than the wet process. However, the latter is simpler and ensures greater durability of the roads.
The difference between the costs of bitumen and plastic, according to research, can be a source of cost saving. A cheap or free supply of plastic waste can considerably reduce costs compared to the cost of obtaining bitumen. Also, the fact that plastic roads have higher endurance and water resistance lowers the costs of maintenance.
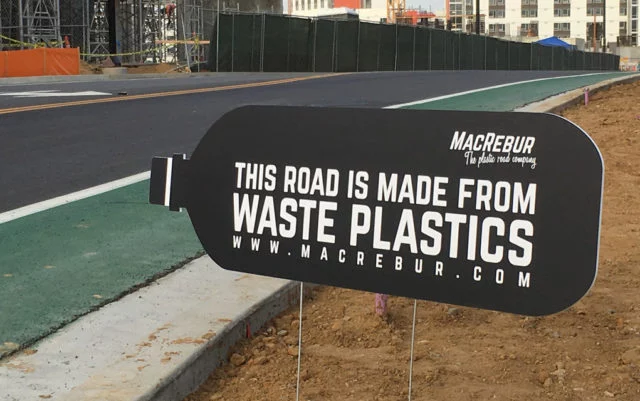
Plastic Roads, Final Thoughts
More than 60,000 miles of plastic roads have been built in India, the country that pioneered in using this type of roads in way back in the year 2000. Not long ago, the United States, South Africa, Mexico, and the Philippines adopted this road construction approach and are already enjoying its merits. Bangladesh should most definitely follow in their footsteps to prevent its roads from being defeated by the adverse effects of the country’s subtropical climate and also, of course, to protect the environment.
Visit our Instagram and Facebook.
Follow The Interlude for more.